3D Printing
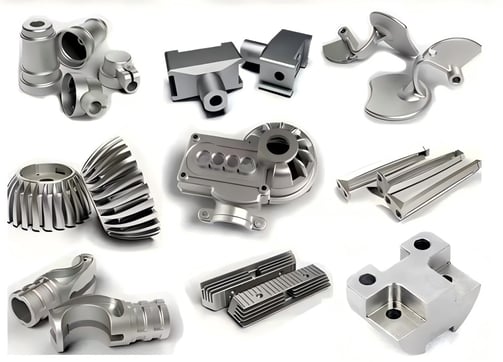
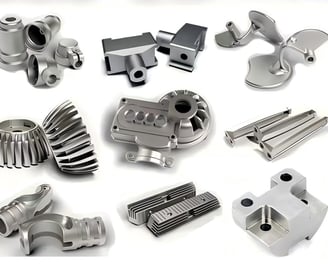
1. Design and 3D Modeling
The process begins with the creation of a 3D model using Computer-Aided Design (CAD) software. Designers and engineers work together to develop a digital blueprint that defines the shape, dimensions, and features of the object.
The 3D model is then exported in a file format compatible with 3D printing, such as STL or OBJ.
2. Slicing the Model
The 3D model is imported into slicing software, which converts it into a series of thin horizontal layers (slices). The software generates G-code, a set of instructions that guides the 3D printer on how to build each layer.
During this stage, parameters such as layer height, print speed, and infill density are configured to optimize the print quality and strength.
What is 3D printing?
3D printing, also known as additive manufacturing, is a revolutionary technology that builds three-dimensional objects layer by layer from digital models. This process enables the creation of complex geometries and customized parts with minimal material waste, making it a game-changer in industries such as aerospace, automotive, healthcare, and consumer products. Below is an overview of the key steps involved in the 3D printing process:
3. Material Selection
The appropriate material is selected based on the application and desired properties of the final part. Common 3D printing materials include:
Thermoplastics: Such as PLA, ABS, and PETG, widely used for prototyping and consumer products.
Photopolymers: Used in resin-based 3D printing for high-detail parts.
Metals: Such as titanium, aluminum, and stainless steel, used for industrial and aerospace applications.
Composites: Materials reinforced with fibers (e.g., carbon fiber) for enhanced strength and durability.
4. Printing Process
The 3D printer builds the object layer by layer using one of the following additive manufacturing technologies:
Fused Deposition Modeling (FDM): A thermoplastic filament is melted and extruded through a nozzle, which moves along the X, Y, and Z axes to deposit material layer by layer.
Stereolithography (SLA): A laser cures liquid resin into solid layers, creating highly detailed and smooth surfaces.
Selective Laser Sintering (SLS): A laser fuses powdered material (e.g., nylon) into solid layers, suitable for functional parts.
Direct Metal Laser Sintering (DMLS): Similar to SLS but used for metal powders, producing strong and durable metal parts.
Binder Jetting: A liquid binding agent is deposited onto a powder bed to bind layers together, often used for full-color prototypes or metal parts.
Advantages of 3D Printing
Design Freedom: Enables the creation of complex geometries that are difficult or impossible to achieve with traditional manufacturing methods.
Customization: Ideal for producing one-off or customized parts without additional tooling costs.
Material Efficiency: Minimizes waste by using only the material needed to build the part.
Rapid Prototyping: Accelerates the product development cycle by allowing quick iterations and testing.
On-Demand Production: Reduces inventory costs by enabling parts to be printed as needed.
Zonda Group's precision machining services have significantly improved our production efficiency. Their commitment to quality and innovation is truly commendable.
John Doe
★★★★★
About
Precision machining solutions for diverse industries.
services
Zonda Group
© 2024. All rights reserved.