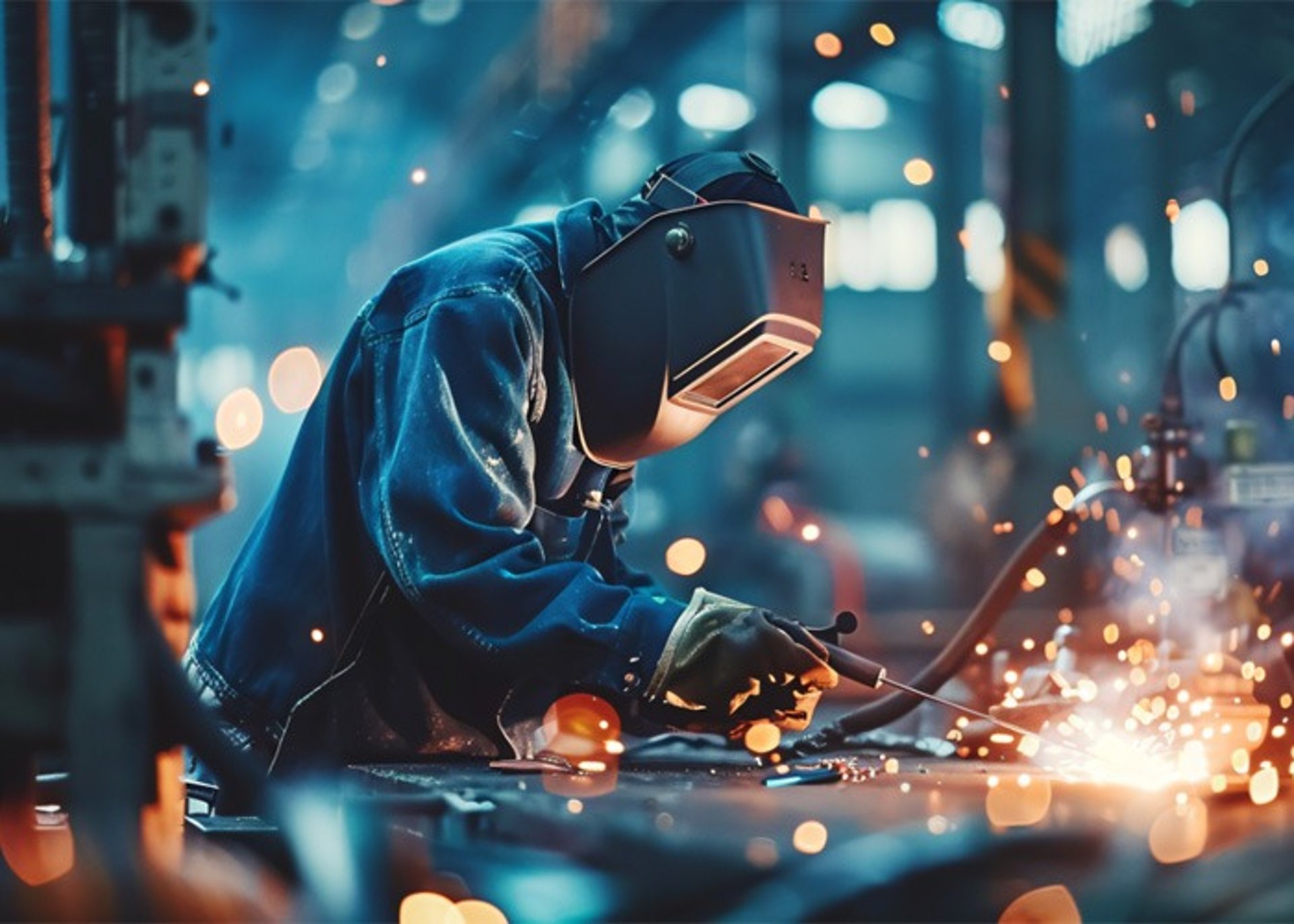
Sheet Metal Processing
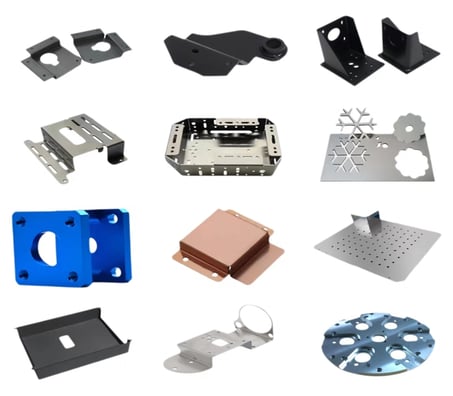
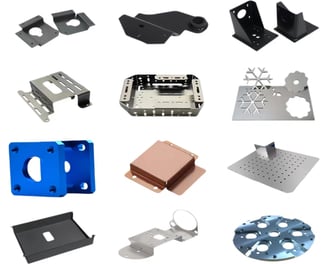
1. Design and Engineering
The process begins with the creation of a detailed design using Computer-Aided Design (CAD) software. Engineers and designers work together to develop a blueprint that specifies the dimensions, tolerances, and material requirements for the sheet metal part.
Design for Manufacturability (DFM) principles are applied to ensure the part can be efficiently fabricated with minimal waste and cost.
2. Material Selection
The appropriate sheet metal material is selected based on the application and desired properties. Common materials include:
Steel: Known for its strength and durability.
Aluminum: Lightweight and corrosion-resistant.
Stainless Steel: Offers excellent corrosion resistance and aesthetic appeal.
Copper and Brass: Used for electrical components and decorative purposes.
Sheet Metal Fabrication
Sheet metal fabrication is a versatile and widely used manufacturing process that involves shaping and manipulating thin metal sheets into desired forms and structures. This process is essential in industries such as automotive, aerospace, electronics, and construction, where lightweight, durable, and precise components are required. Below is an overview of the key steps involved in sheet metal fabrication:
3. Cutting
The sheet metal is cut to the required size and shape using various cutting techniques, such as:
Laser Cutting: A high-precision method that uses a focused laser beam to cut intricate shapes.
Plasma Cutting: Suitable for thicker materials, using a high-velocity jet of ionized gas.
Waterjet Cutting: Utilizes a high-pressure stream of water mixed with abrasive particles to cut through metal without generating heat.
Shearing: A mechanical process that uses a shear blade to cut straight lines in the sheet metal..
4. Forming
The cut sheet metal is shaped into the desired form using various forming techniques, such as:
Bending: Achieved using press brakes or folding machines to create angles and folds.
Stamping: Uses dies and punches to create complex shapes and patterns.
Rolling: The sheet metal is passed through rollers to create curved or cylindrical shapes.
Deep Drawing: A process where the sheet metal is drawn into a die to create deep, hollow shapes.
5. Joining
The formed sheet metal parts are assembled and joined using various techniques, such as:
Welding: Fusing parts together using heat, commonly used for strong, permanent joints.
Riveting: Mechanical fasteners are used to join parts without the need for heat.
Adhesives: Specialized adhesives are used for bonding parts, especially in applications requiring a smooth surface finish.
Bolting and Screwing: Mechanical fasteners are used for detachable joints.
Advantages of Sheet Metal Fabrication
Versatility: Capable of producing a wide range of shapes and sizes.
Precision: Advanced techniques ensure high accuracy and consistency.
Cost-Effective: Efficient processes reduce material waste and production costs.
Durability: Sheet metal parts are strong, lightweight, and resistant to wear and corrosion.
Zonda Group's precision machining services have significantly improved our production efficiency. Their commitment to quality and innovation is truly commendable.
John Doe
★★★★★
About
Precision machining solutions for diverse industries.
services
Zonda Group
© 2024. All rights reserved.